In today’s eCommerce environment, delivery expectations are high and customers expect to receive the best service possible. Unfortunately, not everything always goes as planned and delivery exceptions occur.
Luckily, there are ways to mitigate the impact of unpredictable delays – and even prevent delivery delays – with proper planning and use of technology.
What is a delivery exception?
A delivery exception means that a package is delayed as something unexpected occurs to prevent an order from being delivered on time. Common causes of delivery exceptions include faulty communication with the recipient, poor weather, incorrect address or other label information, shipping label damage, or road blockage.
With the boom in eCommerce businesses and online orders in the post-COVID world, logistics management operations for shipping carriers are not up to speed. Too often, their logistics software is outdated and simply cannot handle the demand that managing delivery exceptions places on the business.
This article takes a look at the key reasons why common exceptions happen, why they are a risk to your business, how to mitigate that risk and better manage delivery exceptions (or even better: eliminate them before they happen!).
What are the different types of delivery exceptions?
Delivery exceptions happen on a daily basis and for a variety of reasons:
7 common causes of delivery exceptions:
- Lost orders
- A delivery driver can’t complete a task
- Federal holidays
- Customs delays for International shipping
- Missing or incorrect documentation
- Traffic accidents
- Inclement weather, a natural disaster, or other unexpected event causing a shipment exception
Lost orders
An order gets lost due to an incorrect address, an issue with a shipping carrier, a problem on a delivery route, missing documentation, or other reason.
Delivery driver is unable to complete a task along the delivery process
This includes being unable to update the expected delivery date, an issue with a recipient’s address, a lack of communication, etc.
Federal holidays
Although a federal or national holiday is not considered a business day, they can cause delays in the delivery date.
Customs delays
International shipping has its own source of exceptions. International shipments usually pass through customs, often leading to unexpected delays.
Missing documentation or incorrect shipment information
This includes damaged shipping labels, missing labels, incorrect addresses, issues with customs paperwork, etc.
Traffic accidents
While most drivers use delivery route optimization software that takes traffic into consideration when planning delivery routes, unforeseen events can easily lead to late deliveries. This can cause a chain reaction for the rest of the deliveries on that driver’s run.
Inclement weather
Severe weather conditions can cause orders to be temporarily delayed or even lost.
While logistics companies can make great efforts to minimize delivery exceptions, they’ll never be brought down to zero. That’s why having efficient and technologically advanced systems in place is critical in order to handle these delivery exceptions, increase on time delivery rates, keeping customer satisfaction rates – and the rate of returning customers – high.
.
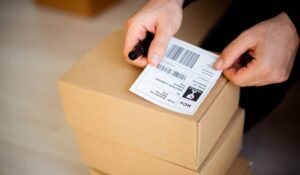
Why are delivery exceptions important?
Think about yourself as a customer. You buy something online and receive a delivery date. As far as you’re concerned, the price and delivery guarantees are to be relied on. After all, you may decide not to purchase if you don’t know how much something will cost or when it will arrive.
And then, your package doesn’t arrive. You didn’t receive an update, you don’t know where it is or when it’s expected to arrive, the delivery dates haven’t been updated – or you may never have received an expected delivery day at all – and you feel like you’re stuck in the unknown.
That’s the issue with delivery exceptions, particularly in eCommerce fulfillment. They leave customers with a lack of answers and most importantly: a lack of consistency. In many cases, an ecommerce business will only contact the customer with shipping information after the shipment is late, or after they have discovered that there is an issue. Worse, customers don’t always see the delivery status, or have an easy way to contact the carrier or delivery provider if something goes wrong.
This is the wrong way to deal with customer service – and the wrong way to help keep customers happy.
How a delivery exception impacts business:
- Inefficiency – managing exceptions is resource intensive and diverts resources that you don’t have to spare. Moreover, many ecommerce businesses – and the logistics or courier companies – lack the resources to handle every delivery exception.
- Wasted resources – every delivery exception causes delays, which in turn cost you potential revenue.
- Loss in overhead – every additional truck roll or delivery run, and every additional minute spent by a dispatcher or support team member, adds up to your overhead bill.
- Bad customer experiences – any exception to an on-time delivery can result in customer churn and bad ratings – even if the fault lay with the customer, or another customer earlier in the delivery run.
Too many companies don’t know how to handle delivery exceptions or keep customers happy when a common delivery exception occurs.
Delivery exception issues
When something goes wrong in the supply chain and a last mile delivery or shipment exception occurs, companies must have systems in place to correct the issue immediately and alert the customer. Hiding behind the delivery exception will get businesses nowhere.
Legacy systems
What happens when a driver reaches his destination, only to find out that it is an incorrect address, due to an incorrect shipping label on the package?
Most legacy systems don’t really support reverse logistics – including allowing drivers to input this data back into the system. This will result in losing inventory if the problematic package goes back into the rotation.
If the missed order gets taken back to the warehouse, then in terms of inventory tracking information, it often enters a black hole: it won’t be re-optimized, put back on the truck and sent the next day. The whole process to resend the package takes a long time and lacks both logic and efficiency.
Manual processes and lack of visibility
When a manual process is used, different steps in the process are easily missed. Reshipments may be prioritized incorrectly (by drop off order for example), if something breaks it can disappear, and in most cases, the company only figures out that there is an issue once the customer complains. Customers often receive an outdated tracking status – or do not even receive any tracking information at all.
The consequences are real. According to one survey of European consumers, 1 in 5 would not order from a retailer again if last mile tracking was not available, or if visibility was otherwise limited.
The bottom line? Customers want reliable shipping services and more importantly, they want complete visibility throughout the process.
What to do when a delivery exception occurs
To deal with delivery exceptions once a shipment is out for delivery, you need real-time visibility. Customers need delivery exception status updates to feel confident in the shipping process and feel rest assured that their order will arrive.
Many logistics technology providers offer real-time notifications that alert the relevant stakeholders to a problem so it can be dealt with quickly, efficiently and cost-effectively.
For example, if a driver or technician is running late, they – as well as the dispatcher and recipient – can be notified via live alerts. Each alert or exception notice can be customized per persona; for example, when a driver is running late, recipients can receive a ‘status exception’ notice, along with a link to reschedule their delivery, or reroute it to an alternative location for convenient pickup according to the recipient’s address.
Logistics providers may want to provide shippers with real-time alerts as well, or alternatively, wait until an issue has been resolved before updating them.
To be useful at scale, these alerts must be sent out via customized triggers which alert the right people with the right exception notice at the right times.
In the case of a late shipment, a provider may move the shipment automatically to the next delivery time slot, or engage a 3PL logistics provider to cover the excess demand.
A parcel shipping delivery might require an automated ‘you’re running late’ alert two minutes before the next scheduled delivery, but a longer on-site service might need a longer 10-minute time buffer between the warning and the time they must leave for their next appointment.
To work, these triggers will rely on speed, accuracy, and customization. The best way to ensure these factors is to use automated delivery exception workflows.
Solutions to a delivery exception
Delivery exceptions are going to occur to all eCommerce businesses. Your response to these delays using delivery management software is what will determine the customer experience and whether or not you are left with satisfied or frustrated customers.
Looking for efficient exceptions management solutions?
Visit Bringg.com/logistics
The carrier needs to find out about delivery exceptions before customers do
Being proactive in responding to every delivery exception is a must for a last mile carrier who wants on time delivery each and every time. When logistics providers can address a delivery exception in real time via automation, they can proactively engage from a customer success standpoint or reroute the package immediately to remain efficient.
On a large scale, this level of service is only possible with automation. When the system can instantly recognize an issue and send out an alert, you’ll be left with a happy customer who knows exactly what to expect.
Automate your exception handling
Optimizing your supply chain through automation tech will help you better manage exceptions. Start by using your historical data to identify the things that go wrong, and address them by creating workflows with automatic responses.
The if/then workflow
These if/then workflows should account for every scenario that you experience with regularity. For example, when customers aren’t home to pick up an order, or when an item is damaged in transit, a smart exception flow will provide drivers with explicit instructions on how to proceed.
These workflows will then trigger alerts and action items as discussed.
For example, if a technician is installing a dishwasher or a white glove delivery service provider is assembling furniture and running late, they should receive an automated alert to wrap up in time to leave for the next stop. If the driver needs more time to complete the service, they can have an option to press ‘I need more time’, which triggers a fallback flow – alerting the next customer of a delay, or pushing the next stop to a later window.
Like most things that work well, these workflows will require both data and technology to run smoothly. You will need to accurately estimate time to deliver, time on site, and time to base for each type of delivery and service, as well as insights into the common issues your delivery operations face, and the factors that cause them.
Predictive alerts to handle delivery exceptions before they come up
Another way to handle a delivery exception is to predict and avoid it.
Predicting a delivery exception requires machine learning and other AI solutions that use algorithms and your historical data to predict when an exception will occur. Then, your system can send out automated alerts to teams in order to prevent the exception: unloading and rerouting large items on a truck filled beyond capacity; alerting drivers when they’re behind schedule in their delivery, and other notifications that can prevent bad delivery experiences and expensive, significant delays.
Delivery exceptions are inevitable to some degree, and operational managers do their best to avoid these situations. But when they do happen, implementing these strategies and technologies will soften the impact to your business, keep customers satisfied, and ensure that delivery issues are the exception rather than the rule.
Have flexible coverage options
If something comes up during the delivery process, having flexibility in your coverage options can be the thing that makes an unforeseen event turn into a manageable event.
By working with multiple carriers, you’ll have the opportunity to outsource if and when necessary and therefore avoid situations in which online shoppers are disappointed and frustrated. DHL delivery exceptions happen as can a Fedex delivery exception or other carriers. Therefore, flexibility is key!
Automated reprioritization vs. getting lost in the warehouse
What happens to an order after a delivery exception?
There are two different options here: getting automatically thrown back in the mix (good) or being dumped back on the shelf in the warehouse (bad). If goods are taken care of immediately and delivery is rescheduled efficiently, the delivery exception will be handled in an appropriate way. This should include visibility for the customer at every stage of the process.
How to manage delivery exceptions efficiently
While digitizing and automating your delivery and fulfillment process will help improve your first delivery attempt rate, delivery exceptions will always occur. The way you handle each delivery exception is what will make or break the last mile customer experience.
Too many eCommerce businesses and the providers that support them are challenged by the sheer scale of shipments at the moment, which limits the time they can spend managing exceptions or optimizing the exceptions handling process.
Without the right technology and support, no eCommerce business can handle their delivery exceptions at scale.
With Bringg’s platform, you’ll have the ability to vet additional capacity and regional coverage. Automated dispatch and routing free up teams to manage exceptions, while our carrier delivery management tools prioritize giving you the ultimate visibility to your customers so that they’ll be satisfied, even when exceptions take place.
Want to learn more about Bringg’s delivery solutions? Let’s chat >>